Soldering is a process that, in the sphere of manufacturing electronics and metal products, cannot be omitted at all. Whether it be in manufacturing advanced electronics such as circuit boards or in creating delicate jewelries, making sturdy and high-quality joinery is always crucial. A material that is instrumental to soldering is what is referred to as flux. For years now, it has been found that the effectiveness of soldering depends on a material referred to as flux. Frequently overlooked, the importance of ‘flux’ cannot be overemphasized because it is an indispensable tool in soldering for the production of clean, efficient, and longer-lasting solder joints. In this all-encompassing article, the author carefully explains the detailed aspects concerning the flux kind, its usage, and significance in soldering procedures.
What is Flux?
Flux in soldering is a chemical cleaner that is often applied in soldering processes to eliminate dirt and oxide layers on the surface, thus enhancing the intermetallic compound bond formation and flowability of the soldiers. In the absence of flux, the oxidation on the surfaces of the metal results in inability to form a strong bond, which ultimately results in forthe formation weak or unreliable connections. Flux is mostly used to help get rid of oxidation layers that might be on surfaces that are touching. It also acts as a glue between the surfaces of the joint to improve the wetting of the solder between them.
Story of Flux in Soldering
The adiabatic use of flux is of very long vintage, it is perhaps as old as the civilization itself. Ancient blacksmiths and metal workers came to learn that materials could remove particles on the surface of the metal, that made them more suitable for welding and increasing the tensile strength of the work piece. He added that over the decades, there has been changes in formulation and use of flux due to the innovations in electronic devices.
At the dawn of the electronics manufacturing industry around late 1800s and early 1900s, new fluxes made from rosin started to come into use. Rosin from the pine resin was also effective and much more convenient to use as cleaning and preparing of the electronic components for soldering. Today there still innovations in formulation of fluxes to provide dedicated fluid for each specific soldering process.
Types of Flux
Even though Flux is available in numerous kinds, each has different formulation with a special use under various soldering settings. The main types of flux used in soldering include:
- Rosin Flux
- Water-Soluble Flux
- No-Clean Flux
- Acid Flux
Rosin Flux
Soldering in electronics majorly employs Rosin flux which is a natural organic substance obtained from pine resin. It is available in three main types:
- R (Rosin): The pure rosin flux for non-critical usage because of its very nature is less reactive than the other more complex forms.
- RMA (Rosin Mildly Activated): Use it for most general electronic soldering work and it contains mild activators for cleaning functions.
- RA (Rosin Activated): Strong activators, suitable for smoothing of heavily oxidized surfaces but needs cleaning after soldering.
Rosin fluxes also offer special feature of eliminating oxides and enhancing solder flow on the joint surface. But they require cleaning after use as they may bring in corrosion and electrical interference residues.
Water-Soluble Flux
Water-soluble flux is prepared from organic acids and other activators as these types of fluxes can be removed easily by washing with water after the soldering process. It offers very good convening and soldering properties, yet there is normally a need to clean after soldering as the flux may leave a residue. It is often employed in instances, where such residues might degrade performance or worse – shorten the device’s lifespan.
No-Clean Flux
Special no clean fluxes allow only a very small amount of residue on the soldered parts which will not corrode the component or assembly, and don’t need to be cleaned. These fluxes are common in situations where a high production rate is required, such as in electronics assembly, and the expense and time necessary to remove residual solder can be high. In fact, no-clean fluxes are designed to offer sufficient cleaning and soldering capability but only a small amount of residue.
Acid Flux
Inorganic flux includes acid flux where various strong acids such as hydrochloric acid or zinc chloride can be present. It is housed primarily for welding non-electrical metals such as plumbing or metal work since its cleaning characteristics are extremely forceful. Acid fluxes are not preferred on electronics since they are damaging to the components for mainly causing severe corrosion.
The Fundamentals of Soldering
it is against this background that one can appreciate just how much is involved with the concept of flux when soldering. Soldering is a technique identified withPaste and is the union of body or two or more metals in which a filler metal (Solder) is allowed to flow and solidify around the meeting area. It is used commonly in all electronics, plumbing, and mostly in the manufacture of any hard metal. There are various parameters that actually affect the qualification of a solder joint which include solder type, the cleanliness of the serves to be soldered, soldering procedures as well as the flux used.
Functions of Flux in Soldering
Flux performs several critical functions in the soldering process:
- Oxide Removal: It is worth knowing that all metal products can be oxidized spontaneously when they are exposed to the air. These oxides prevent solder wetting action as they form a barrier to the soldering material. Flux in this process dissolves these oxides, hence leaving the surface with a clear tongue on which solder can yield to.
- Surface Tension Reduction: Flux lowers the interfacial tension between the molten solder and the base material by causing the molten solder to spread more and cover the surfaces to be bonded with more ease and in the process provide better dissemination and hence better joint strength.
- Heat Transfer Enhancement: As indicated above, since flux enhances the conduction between the soldering iron and the workpiece, it results in increased heat transfer qualification which leads to faster and more efficient heating on the work piece.
- Residue Management: Types of fluxes that are still in use have varying capabilities when it comes to the amount of residue left behind after solder process. Apart from fatigue damage, these residues need to be controlled and dealt with in a proper and efficient way because they can cause corrosion and negatively affect the soldered joint’s durability.
Applications of Flux in Soldering
Flux is used in various soldering applications, each requiring specific types of flux for optimal results:
Electronics Soldering
- Printed Circuit Boards (PCBs): Solder flux is critical in construction as well as in rebuffing of PCBs for the purpose of making connections in the component and trace way.
- Surface Mount Technology (SMT):That is why in SMT, flux plays an important role in ‘sticking’ the components on the PCB before the soldering process, which helps to avoid such failures as tombstoning and insufficient number of solder interconnections.
Plumbing
- Pipe Joints:The instance where flux is applied is in plumbing, where it is employed to prepare the pipeline joints for soldering so as to get a leak-proof joint formed.
Metalworking
- Jewelry Making: In soldering of precious metals, flux is applied to guarantee firm but sleek and untarnished joins in high priced jewelry products.
- Automotive Repair: In automotive applications, flux is used in soldering operation, where it serves to ensure that pieces fit together mechanically as well as electrically.
Advancements in Flux Technology
Flux technologies are a relatively progressive field that has experienced enhanced developments in the recent past due to its increasing application in the areas such as reliability, environmental issues and performance. Some of the latest developments include:
- Lead-Free Soldering Flux
- Some changes in operations have been made to use flux for lead free solders due to pollution laws that have been put in place such as RoHS. Such fluxes provide proper wetting and bond strength despite the higher melting points characteristic of lead-free.
- Low-Residue Flux
- It was also observed that with increase in the usage of no-clean fluxes there has been continuing improvement in the formulation so that they form even less of a residue thus eliminating the need for cleaning after soldering and hence controlling the likelihood of corrosion and electrical interference.
- Eco-Friendly Flux
- Organically clean fluxes that do not have chemicals such as halides and VOC or volatile organic compounds are gradually being advanced. It provides them, same performances similar to those conventional fluxes and it decreases the environmental pollution level.
- Nanotechnology-Enhanced Flux
- Coating formulations have benefited tremendously from nanotechnology, which has enabled manufacturers to come up with new fluxes with significantly improved wetting characteristics and thermal stability. These fluxes improve joint durability, thermal stability and mechanical strength of solder joints particularly in high density and high performance electronic devices.
How to Choose the Right Flux
Selecting the appropriate flux for your soldering project depends on several factors:
- Application: Jotted some aspects to be considered regarding the type of metal and components sharing the joint that is to be soldered. Stock types for electronics for instance include rosin or no-clean flux while plumbing or any form of metalwork may require acid flux.
- Residue Requirements: As conditions for post-soldering cleaning check if it is possible. In critical system application, water-soluble flux may be required to guarantee that any remaining impurities are cleaned off.
- Soldering Environment: The operating environment defines the temperature and humidity levels and these factors should be evaluated due to their influence on the flux performance.
- Compliance: It needs to be ensured that the applied flux conforms to the market standards and requisite norms especially for electronics applications.
Best Practices for Using Flux in Soldering
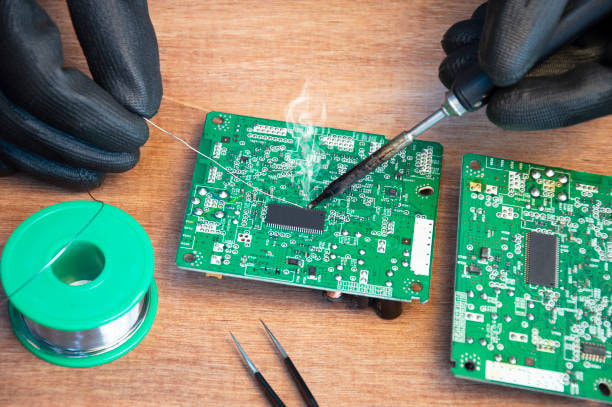
To achieve the best results in soldering, it is essential to follow best practices when using flux:
Choosing the Right Flux
- Choose the right fluxing type based on the use, solder alloy intended for use, and kind of cleaning that will be used. For instance, you may use the rosin flux for usual work on the electronics parts, water soluble for situations when you need to wash off the flux, and no clean flux for the situations that will use an automatic system.
Applying Flux Properly
- To prevent heat from damaging the metal, one should ensure that the flux is applied uniformly in the surface areas to be soldered. Do not apply too much flux as it will build up and cause formation of oxides and/ or salts that will in-turn cause corrosion.
Controlling Heat
- Take precaution while using the flux particularly while soldering as this is capable of emitting toxic fumes that can interfere with the soldering process besides emitting fumes that can burn the skin. Soldering iron at the correct temperature when soldering and don’t heat for a long period.
Cleaning Residues
- In case the used flux produces residues, wipe them off after soldering with the right cleaning detergents or solvents available in the market. This step is important as it helps in the elimination of any corrosive action that may act on the soldered joint with the aim of reducing the reliability.
Storing Flux
- Proper storing of store flux is said to involve storage in an area that has low temperatures and away from humidity. Make sure that the containers are properly closed to minimize the risk of spoilage due to compounding and moisture.
Challenges and Solutions in Flux Use
Despite its benefits, the use of flux in soldering comes with challenges that need to be addressed:
- Residue Management
- Some effects of flux residue include corrodal attack as well as electrical disturbances which affect the reliability of circuits. This issue can be eliminated wherein no-clean or low residue fluxes should be used in the manufacturing process. For use as applications, be certain that the intended cleaning mechanism is efficient enough.
- Compatibility with Lead-Free Solders
- Lead-free solder alloys are reported to have higher liquidous temperatures and different wetting properties than lead bear solders. Closing it is advisable to make sure that the flux used is ideal for the lead-free alloy to ensure that joints made will be ideal.
- Environmental and Health Concerns
- Fluxes can be invasive and may also act as carriers of environmental and health risks such as hazardous substances. Choose green fluxes whenever it is possible and follow the correct flux usage protocols when applying hazardous fluxes.
- Flux Activation and Deactivation
- It is important to recognize what makes flux active or inactive and when this requires modification. Some products such as activated fluxes contain relatively high cleaning capability but they need good rinsing. The residual deposits of inactivated fluxes should be non-corrosive and non-conductive.
The Future of Flux in Soldering
Flux technology is expected to continue being developed for soldering applications, in a bid to provide improvements over the existing problems. Key trends and innovations to watch for include:
Smart Flux Formulations
- The foreseeable future sees fluxes being developed with additional properties like capability for cleaning, and reactivity that could be monitored in real-time regarding the quality of solder joints. These could potentially change traditional soldering practices and enhance the dependability of the device.
Integration with Advanced Soldering Techniques
- Due to continuous advancements in soldering technology introducing Laser soldering and Robotic soldering among others, there is a need to develop special fluxing formulations for the new technologies in order to enhance efficiency in soldering.
Sustainability and Eco-Friendliness
- The trend towards one-pot reactions and green chemistry will further promote the creation of fluxes that will offer better results and also conserve the environment. This also entails rejecting non-degradable substances and hazardous chemicals and embracing renewable and biodegradable materials.
Enhanced Performance for High-Density Electronics
- As the electronics devices being designed are more complex and with compact size, then formulations of fluxes will have to better address high density application and high performance electronics devices. These advancements will be made in an attempt to gain better wetting, to minimize formation of voids and to guarantee superior electrical and thermal conductivity even in immensely harsh conditions.
Case Studies and Real-World Applications
To illustrate the impact of flux in soldering, let’s explore a few case studies and real-world applications where flux played a critical role:
- Consumer Electronics Manufacturing
- In the formation of smartphones and tablets specifically, this no-clean flux is chiefly used owing to the effectiveness of the no-clean process and the feasibility of the mere removal of residual solder. One of the customers who designated a global smartphone company applied a no-clean flux with improved formulation that reduces voiding in solder joints thereby making the devices more reliable and minimizing failure rates.
- Automotive Electronics
- Automotive electronics have stringent requirements for solder joints because of the conditions under which their solders operate. automotive supplier has replaced the lead containing solder and also the natural rosined based flux to a lead-free solder and a suitable water-soluble flux which enhanced the joint strength and reduced the number of joint failures due to thermal cycles and vibrations. Cleaning after the soldering process was meant to rid the board of any remaining flux residues which might otherwise cause long term damage when exposed to moisture.
- Medical Devices
- In the context of medical devices manufacturing the solder joint performance-ability or cleanliness is critical. A medical equipment maker used a low residue soldering no-clean flux to assemble a critical life monitoring device. Another thing was that the low-residue character of the flux allowed avoiding further cleaning after soldering all the devices and thus, decreasing the costs of production and guarantee adherence to the strictest requirements.
- Aerospace Applications
- Avionic electronic equipment requirements include outlaws of variations in temperature and vibration. An aerospace contractor used an auto-clinable rosin-based soldering flux to bring together tightly toleranced parts. The flux possessed good wetting characteristics which ensured good joints, besides the failure towards corrosion would mean a lifetime reliability which is crucial on aircraft and satellite systems used for space missions.
Conclusion
Because flux is a vital element in soldering and the quality of the solder joint that is produced is crucial in determining the reliability and durability of solder joints, it is necessary to understand their function. Starting with the simple use of flux for oxide removal and ending with the most advanced fluxes for the environmentally friendly and high-performance application in electronics, automotive, medical devices, and aerospace industries, flux that was once a simple reagent has become truly indispensable.
Reading the types of flux and each kind of role so as to have suitable methods applying is very essential in getting desirable soldering outcomes. With the current world developing in flow, technology also progresses, the need to deliver high performance and at the same time being environmentally friendly will continue posing new challenges to the flux industry supplying new products that meet the current standards of manufacturing industries.
When assisted by the latest knowledge in flux technology and following good practices, solder joints of good quality are a possibility and significantly improves reliability of any manufactured product. Fluxes are known to play a significant role in this process; small-scale or an electronics hobbyist to a professional assembler or a large manufacturer, having the right flux means a successful soldering job.